电池在生产过程中,空气中会存在微尘颗粒和杂质,并且正负极上也含有粉尘及毛刺,这些因素会使电池内部容易发生物理接触而诱发短路,使电池性能受到极大的影响,严重时甚至可能使电芯充不进电,造成“无电”电芯。锂离子电池厂家在完成电芯组装工序后,会对其进行在高压下的短路测试,主要判断电芯内部是否存在异物颗粒造成的短路,以便挑选出容易短路的电芯。由于隔膜都存在一定的耐电压强度,当加载电压过高时能够击穿隔膜,形成漏电流。因此,首先电芯绝缘测试电压要低于击穿电压。当正负极之间不存在异物时,在测试电压下漏电流小于规定值,判定电芯合格。而如果正负极之间存在一定尺寸的异物,隔膜会被挤压,正负极之间的间距减小,击穿电压下降,如果还加载相同电压,漏电流可能超过设定的警报值。通过设定测试电压等参数,就可以统计分析判断电芯内部的异物尺寸。一般情况下,隔膜越薄,耐电压强度越低,测试电压理论上也应该更低。隔膜含水量过高时也容易形成较大的漏电流。如果测试电芯内部存在异物,可能造成内部短路,电芯被击穿,如图1所示。

因此,裸电芯的绝缘耐电压测试是锂电池生产过程检验的关键环节,可以检测出不合格产品,提高最终电池产品的安全系数。本文以短路率为出发点,重点统计并研究了锂电池各个制作环节中的电芯短路率,并进行了原因剖析,为电芯制作中的短路率控制提出了指导方向。使用叠片式进行电芯组装,容量为5Ah,正极材料为三元523;负极材料为石墨;隔膜采用12个批次,共计50个样品(详见表 1);铝塑膜;电解液。
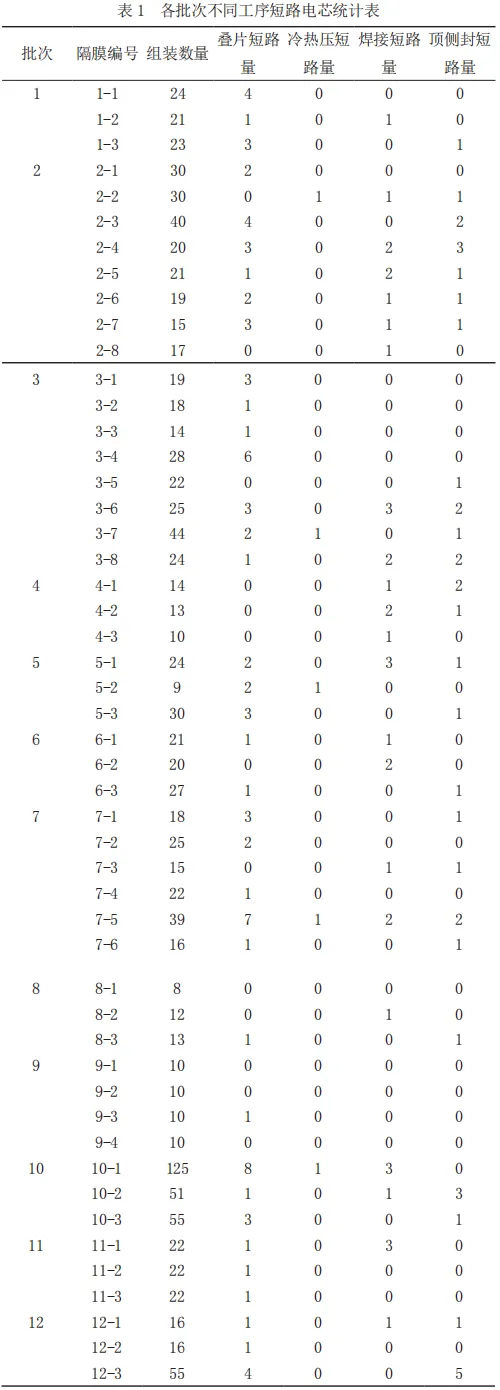
按照电池容量,使用半自动叠片机对电芯进行组装,使用转盘式冷热压机对电芯进行冷热压整形,随后使用超声波极耳焊接机进行极耳焊接,最后使用四工位顶侧封机对组装好的电芯进行顶侧封。使用绝缘电阻仪,对电芯不同环节的短路情况依次进行测试,设置检测电压为200V,电阻值为20MΩ。在相同制作环境下,使用相同的正负极材料和电解液,对12个批次、50个隔膜样品进行了锂电池制作,并对锂电池不同制作环节的短路率进行了统计,得出以下结论。(注:上表各批次中,隔膜型号用相应编号代替。)从以上数据分析,总共组装1214电芯,其中叠片环节短路86块,短路率7.08%;冷热压环节短路5块,短路率0.41%;极耳焊接环节短路36块,短路率2.97%;顶侧封环节短路38块,短路率3.13%。各环节短路率高低依次为叠片>顶侧封≈焊接>冷热压。将微短路的锂电池拆开,可以发现隔膜上会出现黑点。如果黑点位于隔膜中心附近,很大概率是由于粉尘击穿造成的。锂电池在生产制造过程中,空气中的粉尘或者制成时极片、隔膜沾上的金属粉末都会造成电芯内部微短路。杂质造成的微短路所引起的不可逆反应,是造成个别锂电池自放电偏大的最主要原因。
极片在使用前,要使用特定模板裁切成规定尺寸。裁切过程中不可避免会出现极片掉屑或者毛刺,这些异物在叠片时会有一部分卷入电芯中,夹杂在正负极和隔膜之间,存在内部微短路风险。将微短路的锂电池拆开,当发现锂电池的隔膜上出现的黑点处于边缘位置占多数,便是极片分切过程中产生的毛刺引起的。

在叠片过程中,隔膜应该完全包裹住正负极极片,并且负极片的尺寸略大于正极片。在某些情况下,隔膜的纠偏过程出现问题,造成隔膜无法完全包裹住正负极极片,隔膜向一端偏移,造成正负极极片直接接触,形成短路。
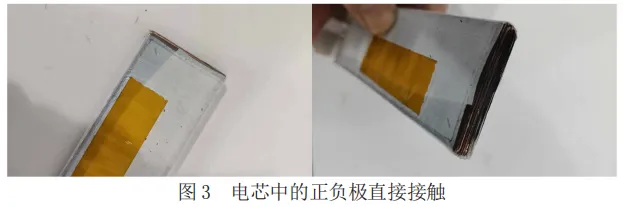
(1)毛刺。叠片工序没有检测出短路的电芯,冷热压工序中,在强制外力的作用下,电芯被挤压,内部空间发生压缩,之前存在于内部的毛刺这时很可能刺穿隔膜,造成短路。(2)由于隔膜的机械强度不够,在冷热压环节,强制施加外力的条件下,有可能造成隔膜被撕裂或者穿刺成大孔,正负极接触,形成短路。(1)传统的超声波焊接工艺,焊接面积小,焊接强度差,特别容易出现虚焊现象。在超声焊接过程中,容易使集流体处金属屑飞溅至极耳胶和电芯主体上。飞溅到极耳胶处的金属屑因瞬间高温粘结在极耳胶上,无法清除,在后续电芯封装中,使极耳与铝塑膜外壳导通引发短路。
(2)叠片电池由多片正负极组成,容量越高,电芯越厚。极耳焊接时,为了将所有裸露的集流体焊接在一起,位于电芯外侧的极耳会被一定程度的向外拖拽,这就可能造成隔膜无法完全包裹住极片,存在正负极接触的可能。

(1)铝塑膜充壳时,厚度不能完全符合电芯要求,存在入壳困难的可能性。入壳时在边角处可能造成电芯挤压,导致正负极接触,形成短路。(2)顶封相比侧封,如果封头温度过高,容易造成铝塑膜中的铝箔和正负极极耳导通,形成短路。针对可能造成电芯短路的各个制作环节,可以从以下几个方面重点着手,降低电芯的短路率,提高电芯制作水平。(1)使用模板对极片进行裁切后,以及在放入料盘之前,尽量去除极片上出现的掉屑或毛刺,降低内部微短路风险。(2)电芯制作过程中,严格控制空气中的粉尘和杂质的含量,尽量避免异物的混入。(3)叠片过程中,时刻调整纠偏电机,调整隔膜的限位装置,使隔膜完全包裹住正负极极片,避免两者错位造成接触,防止电芯顶端或底部正负极短路的形成。(4)焊接极耳时,设置好焊接电压和触发时间等参数。如果电芯较厚,可以将极耳焊接在电芯中间部位,防止极片被过度向外拖拽。(5)顶侧封环节,设置好热封温度以及热封时间,防止由于热封时间过长,造成过封。(6)铝塑膜冲壳时,严格根据电芯厚度进行冲深,使铝塑膜完全包裹住电芯,防止由于冲深不够造成电芯边角处挤压。(1)隔膜要有足够高的机械强度,抗刺穿能力也要强,尤其是在冷热压环节,防止隔膜由于机械外力造成撕裂。(2)隔膜的物理绝缘性要高。击穿电压在合理范围内,应该尽可能的高。同时为了防止毛刺穿刺隔膜,隔膜中大孔在孔径分布中所占比例应该尽可能低。(3)可以使用涂层隔膜,在增强热稳定性的同时,也能够适当增强机械强度,降低电池的短路风险。
来源:旺财锂电