目前手机电池主要采用卷绕工艺。卷绕工艺是将正极、隔膜、负极以卷绕方式组合成形的储能单体,称为卷绕电池。单个卷绕电池也称为电芯,电池业内人士称为卷芯。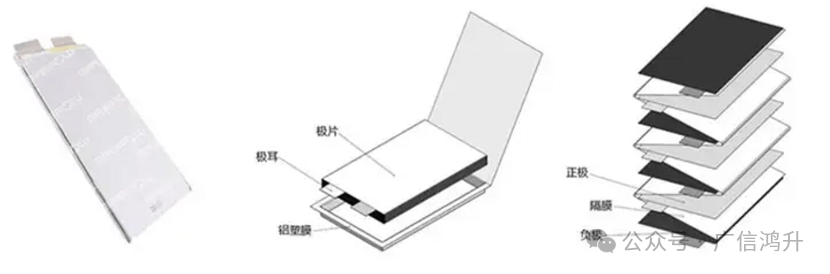
电池制造工艺主要分为叠片工艺和卷绕工艺两种技术路线。卷绕工艺和叠片工艺在电池制造中有显著的区别,主要体现在工艺原理、电学性能、机械应力、能量密度设计等方面。叠片工艺:将正负极片裁剪成所需尺寸,然后与隔膜叠合在一起,形成小型电芯单体,再将小电芯单体叠放并联形成电池模组。这种工艺的极片裁切主要采用模具冲切和激光切割两种方式。卷绕工艺:通过固定卷针将正极极片、隔膜和负极极片根据一定顺序卷绕,并挤压成圆柱形或方形。极片的尺寸和卷绕的圈数由电池的设计容量决定。
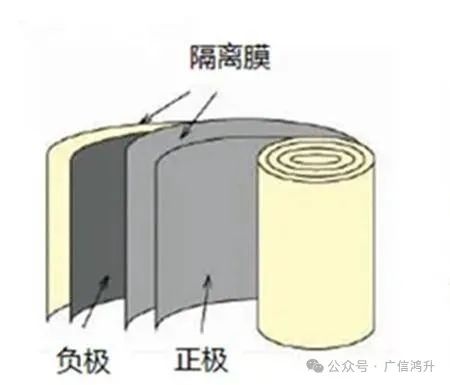
内阻:叠片工艺制造的电池内部电阻较低,因为多个极耳并联焊接,减少了锂离子的迁移路径,从而改善了电芯的发热情况,延长了电池的使用寿命。循环寿命:叠片工艺的电池具有较好的散热性能,支持均匀分布热量,而卷绕工艺的电池由于结构问题,散热不均匀,容易导致容量衰减较快。电极片机械应力:叠片工艺制造的电极片受力均匀,不易损坏,而卷绕工艺在弯折处容易产生应力集中,可能导致电池结构性破坏和短路。能量密度:叠片工艺能更好地利用封装空间,支持更高的能量密度,而卷绕工艺由于电极片弯曲的结构和双隔膜结构占据空间,能量密度较低。叠片工艺:优点包括低内阻、良好的散热性能、均匀的机械应力分布和高能量密度设计。缺点是工艺复杂,成本较高,电芯一致性差。卷绕工艺:优点是效率高、工艺简单,但缺点是内阻高、散热不均匀、机械应力集中和能量密度较低。
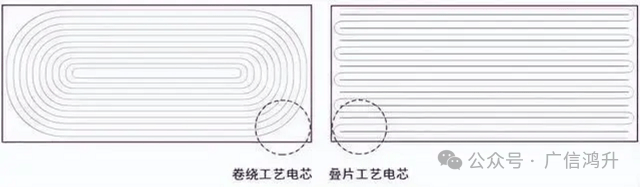
目前中国电池企业的主要技术方向以卷绕为主,但随着叠片技术的进步,大量电池企业开始进入叠片领域。叠片工艺电池正成为发展趋势,受益于先进自动化设备和流程设计,叠片工艺良率得到有效提升。目前国内主流技术路线为Z字型叠片,切叠一体机能够较大程度提升叠片良率,从而逐渐取代传统的 Z 字型叠片。切叠一体机将极片使用冲压模切/激光热切、Z字型叠片机、贴胶热压机三类机型进行整合,能够简化中间工序、减少磕碰,从而提高良率。此外,叠片技术也在持续迭代,叠片效率提升显著。长期以来,叠片受制于效率这一发展瓶颈。目前国内叠片机厂商均注重提升叠片速度,如利元亨高速动力切叠一体机目前最优叠片速度 0.15s/pcs(三工位,即单工位为 0.45s/pcs),正在开发整机0.125s/pcs 的超高速叠片工艺,先导智能切叠一体机最 高叠片效率达800PPM(0.075s/pcs),切叠稳定效率为 0.45s/pcs(单工位),叠片效率的提升是取代卷绕工艺的关键。由于卷绕工艺电池存在能量密度瓶颈,随着叠片技术的持续迭代和工艺效率的显著提升,叠片工艺电池优势不断凸显,将具备更为广阔的市场前景。
手机不使用叠片电池的主要原因包括技术难度、成本、体积和重量等方面的问题。首先,叠片电池虽然具有较高的能量密度和循环寿命,但其制造工艺复杂,技术难度较大。叠片电池需要精 确控制每片电池的厚度和位置,以确保电池组的整体性能和安全性,这增加了生产难度和成本。其次,叠片电池在手机上应用时,会面临体积和重量的限制。手机内部空间有限,叠片电池的复杂结构可能会占用更多空间,导致手机变得更厚或更重,这不符合当前手机设计追求轻薄的趋势。此外,叠片电池在市场上的应用主要集中在车用锂电池领域,而不是消费电子设备如手机。车用锂电池需要更高的能量密度和安全性,而手机电池则更注重便携性和续航时间。因此,叠片电池在技术成熟度和市场应用方面尚未完全适应手机的需求。综上所述,虽然叠片电池在某些领域表现出色,但由于其在手机应用中的技术难度、成本和体积重量等方面的限制,目前尚未成为手机电池的主流选择。